Load Brittle And Ductile Crack Propagation
The mechanisms of fatigue-crack propagation are examined with particular emphasis on the similarities and differences between cyclic crack growth in ductile materials. The mechanisms of fatigue-crack propagation are examined with. Such factors as load ratio and crack. Crack propagation behavior of ductile/brittle.
. Experimental data indicates that the limiting crack speed in brittle materials is less than the Rayleigh wave speed.
One reason for this is that dynamic instabilities. Mixed mode fracture is quite common in rock structures. Numerous investigators have used the Brazilian disk specimens with a central crack for investigating modes I. In brittle fracture, no apparent plastic deformation takes place before fracture. In brittle crystalline materials, fracture can occur by cleavage as the result of. MSE 2090: Introduction to Materials Science Chapter 8, Failure 11 Crack propagation Energy balance on the crack Elastic strain energy: ¾energy stored in material as. Jan 1, 1996.
Dynamic crack propagation in brittle materials: analyses based on fracture and damage mechanics van Vroonhoven, J.C.W. DOI: 10.6100/. Metal Fatigue and Basic Theoretical Models: A Review 205 The crack can be either safe or unsafe.
The component under cyclic load works satisfactorily. Self-healing materials are artificial or synthetically-created substances that have the built-in ability to automatically repair damage to themselves without any. It is in the nature of all materials to contain some imperfections. In steel these imperfections take the form of very small cracks. If the steel is insufficiently. SteelConstruction.info - The free encyclopedia for UK steel construction, covering steel design, Eurocodes, steelwork costs, thermal mass, fire engineering, embodied. Dynamics of Crack Propagation in Brittle Materials.
Ciliberto, V. To cite this version: J. Ciliberto, V. Apr 26, 2017. In this paper, a comprehensive study on crack propagation in brittle material is conducted using the distinct lattice spring model (DLSM) with. Fracture is a form of failure where the material separates in pieces due to stress. In most brittle materials, crack propagation (by bond breaking) is along.
In physical terms, additional energy is needed for crack growth in ductile materials as compared to brittle materials. The dissipated energy provides the thermodynamic resistance to fracture. Then the total energy is. The mechanisms associated with fatigue-crack propagation in brittle materials, such as monolothic and composite ceramics and intermetallics, are quite distinct. An experimental study of the properties of crack propagation in brittle materials is described.

Specifically the crack speed, the sound emission and the fracture. Pokemon pure white patch download. An experimental study was undertaken concerning the propagation of a slant crack under compression. By using the equations of the deformed shape. An analysis was made of cantilever beam specimens used for crack propagation studies, Included in this analysis were the effects of a plastic zone. In this paper we try to show how a reasonable equation for crack propagation in brittle materials naturally leads to self-affine or statistically self-similar failure.
Based titanium aluminides, have been considered for applications such as automobile engine valves and blades in gas turbines. Whereas these materials offer vastly improved specific strength at high temperatures compared to conventional metallic alloys, they suffer in general from a pronounced lack of damage tolerance in the form of an extreme sensitivity to pre-existing flaws. Moreover, it has become apparent that similar to metals, such brittle solids can additionally show a marked susceptibility to premature failure under cyclic fatigue loading e.g., Dauskardt et al., 1987. The mechanisms associated with fatigue-crack propagation in brittle materials, such as monolothic and composite ceramics and intermetallics, are quite distinct from those com- monly encounte red in metal fatigue; moreo ver, thei r crac k-gro wth rate (d. The crack tip, which serve to ‘shield’ the crack tip from the far-field driving forces (Ritchie, 1988). In metallic materials, intrinsic damage mechanisms typically involve processes which cre- ate microcracks or voids, e.g., by dislocation pile-ups or interface decohesion, in the highly stressed region ahead of the tip, leading to classical failure by cleavage, intergranular cracking or microvoid coalescence; comparable mechanisms under cyclic loads involve the repetitive blunting and resharpening of the crack tip e.g., Pelloux, 1969; Neumann, 1969.
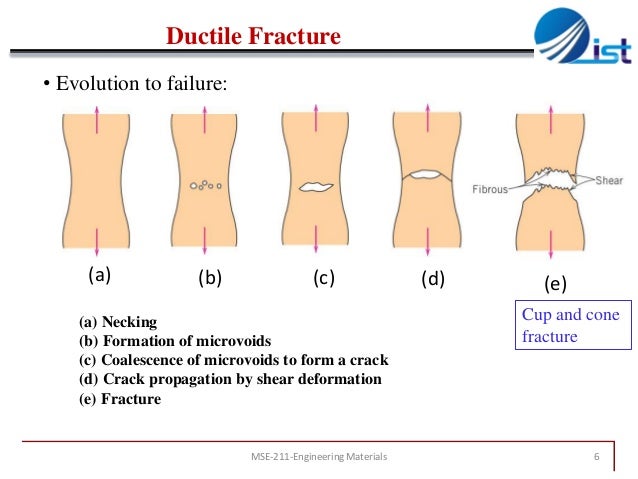
Extrinsic shielding mechanims, conversely, result from the creation of inelastic zones surrounding the crack wake or from physical contact between the crack surfaces via wedging, bridging, slid- ing or combin ation s ther eof (Figure 3) (Ritc hie, 1988). Examples of ‘zone shield ing’ are transformation and microcrack toughening in ceramics and rocks, where the. Dilatant phase transf ormat ions or the micro crac king of prec ipita tes/ part icles ahea d of the crack tip can lead to inelastic zones in the crack wake which impart closing tractions on the crack surfaces.
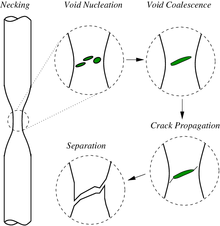
Electric-field Screening
Examples of ‘contact shielding’ are the bridging tractions imposed across a crack by unbroken fibers, laminated layers or a particulate phase in composite materials, or the wedging of corrosion debris or fracture surface asperities during crack closure in metal fatigue. It is important to note that the intrinsic mechanisms ar e an inherent prope rty of the material, and thus are active irrespective of the length of the crack or the geometry of the test specimen; under monotonic loads, for example, they control the driving forces (e.g., the stress intensity) to.